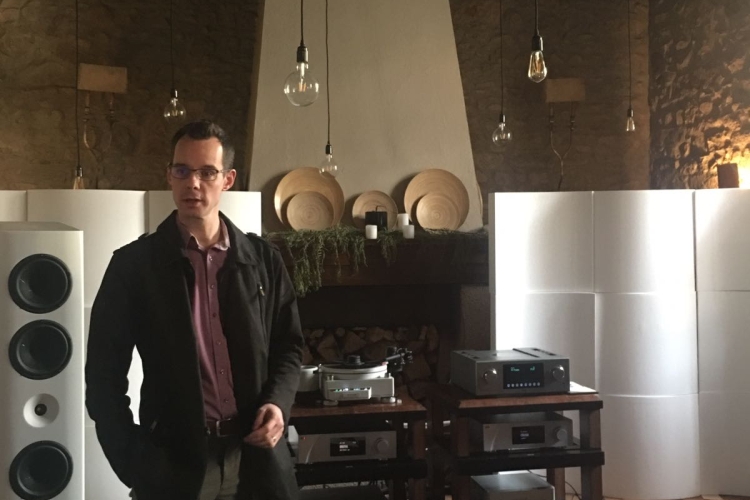
When Cayetano picked me up from the airport in Spain for a drive to the Hotel Convent San Roque in Bilbao for coverage of the 2018 Enosound show, there was another person in the car who he was also driving to the show. That person was Raphael Pasche, one of the designers of CH Precision. We started chatting and pretty soon we agreed that it would be a good idea to do an interview about CH Precision.
HFA: Raphael, what is your position at CH Precision?
Raphael: I am one of the designers. There’s Florian, head designer and Project Manager and also the founder of the company, who puts the skeleton of the products together. We then as a team meet and build the whole body around the skeleton. I am the hardware designer, translating the specifications of the product to be into an electronic circuit and from there into printed circuit boards. When the circuit boards come back from Production, we spark them up and start testing them. That’s an exciting part.
HFA: Because they sometimes burst out in flames?
Raphael: Haha yes that always happens! Nah just kidding, that doesn’t always happen. No, the exciting part is to get sound from A to B and to test it to see if it actually measures up and complies with the specs that you want to achieve. Then there’s a Mechanical Engineer, with whom there is a bit of ping pong, in the sense that he will come up with a mechanical constraint, to which I will fit my board and re-send it to him, and he makes sure that everything aligns properly.
The beautiful garden of Hotel Convent San Roque, where the interview took place.
HFA: What sets CH Precision apart from other high-end brands?
Raphael: There are a few technical aspects to this. CH Precision focuses purely on symmetrical and fully discrete-transistor-based designs, there are no op-amps in the signal chain. All stages except for the power amp output push/pull stage, are Class A. On a more practical level, all components are built around a modular architecture. All components have card slots in which you can fit option cards, which allows the customers to tailor the units to the needs of their system. This does not only allow the customer to customize their units, but it also allows us to develop new boards. Thanks to this, the equipment does not become obsolete and is future-proofed. Another important aspect is that the configuration of the units can be changed. Let’s say you start with a stereo amp with two input cards and at some point, you think it would be nice to go mono, what you do is to buy a second amp without input cards and just move one of the two existing ones to the new amp. Then, from the front panel buttons (or tablet), simply select mono instead of stereo, and you’re done. The unused channel turns off and the entire capacity of the power supply is available for a single channel. The amps can also be bridged, or used for bi-amping. A particularly unique aspect is that the balance between local and global feedback can be set in 6 steps for the A1 (0, 20, 40 60, 80, 100%) and even 11 steps for the M1. When bi-amping this means that you can even choose different settings for the bass and treble ranges. A final specificity that we have in our designs is the capability to go true mono, in all the sources: the phono stage, the line preamp, and the DAC are all single boxes. But if you take the phono stage as an example, you can get a second phono stage, take out one of the input cards, and put it in the second chassis, dedicating one chassis per channel. Then, if you want to go to the extreme of what we can do, you can add external power supplies. So, from 1 box, you can go to 4 boxes for the phono preamp. The exact same applies to the line stage. The DAC can be extended by using two more C1 chassis, each catering to one channel while the main unit is the dedicated digital section. Each of these 3 boxes can then be outfitted with an external power supply, resulting in 6 boxes and that is the ultimate converter that we do. What we do here is to allow a customer to always strive for better, while keeping the units that they have already purchased. You can just grow your system, as you go along.
HFA: It’s very flexible.
Raphael: Indeed!
HFA: When deciding how to voice the products, do you rely more on specifications or more on listening?
Raphael: It’s obviously a combination of the two, but we are based on measurements and a scientific approach. We are engineers, that think structurally and scientifically. We systematically try to find the restrictions or constraints of what we have already done. When you are able to isolate where the restraint is, then you move on to the next, and so on. The aim is to get to to the point where there are no more restraints. At CH, we approach these matters with a very scientific and logical mind. Then we think we are very close to having very good sounding equipment before we’ve listened to it. Then, obviously, we do listen to it, but we’re not going to spend months tweaking it. I think there are quite a few things that we don’t know and we modestly say, ok, there are things we can hear but don’t know how to measure. In this industry, it has been quite widely accepted that what counts is bandwidth, distortion, and noise. But it seems that there is a lot more than that. Nobody has actually developed a piece of equipment that allows you to measure enjoyment.
HFA: You can hear it, but you can’t measure it. Do you use any exotic components?
Raphael: What we do is we use industrial components. Good, reliable components such as metal film resistors, polypropylene capacitors. These are components that you find in all sorts of designs, not something completely esoteric and specific for audio, or designed especially for us. On some occasions, you have no choice and you need to get something designed specifically for you. Power transformers or special capacitors for in the phono stage, things like that.
HFA: What about the transistors?
Raphael: They’re totally standard transistors. I think it’s the way forward, because, first, these components have been designed to be extremely reliable, they’ve been used forever. On top of it, they are not going to go obsolete. This is why we try to be as neutral as we can when the component choice is concerned. But it’s not like we just use any components, we make very conscious decisions.
HFA: Do you do any component matching?
Raphael: We never pair any components. We design the circuitries such, that pairing doesn’t matter. When the pairing does matter, then you have a circuit that is sensitive to this. Make a circuit that is not sensitive to it, that’s the scientific approach. The transistors in the power stage are special transistors, I would say. They are industrial, in that they don’t have 3 legs, but 5. The first 3 legs are the normal base, collector, and emitter and the other two are connected to a diode which is actually on the dye, the same dye as the transistor. When the transistor heats, the VBE voltage will reduce, just like the diode will reduce the voltage across it if you run some current through it. By doing so, you’ve created a thermometer. This allows us to create what we call Exact Bias, which is a way to control the bias of the amp depending on the temperature of the transistor. If you drive it hard, it will reduce its VBE which means it will increase the current going through it and you reduce the bias at the front to compensate for it. So, you make it insensitive to mains voltage, ambient temperature and to how hard you drive your amp. So, you try and make it as constant as possible.
HFA: In my experience, Bridge Mode is not by definition the better solution, how do you view this?
Raphael: A lot of people are criticizing bridge mode, but our designs are truly bridged with the exact same amount of components meaning that there is no propagation delay. The difference between bridge mode and, mono, let’s say, is that with mono, the speaker connects between plus and ground, with an output impedance creating the damping factor, the ratio between the output impedance and the load. Now, if you put your amp in bridge mode then you’ve got two outputs, both of which have an output impedance, so you’ve got double the impedance and thus a lower damping factor. Because we have control over the feedback, we can simply raise the amount of global feedback to drop the output impedance of both your amps to give back the same amount of damping factor that you used to have before. In doing so you counteract the bad effect of the bridge mode. That’s one use for the feedback control. Another use, obviously, is that you can tailor your amplifier to the connected loudspeaker.
Raphael in conversation with audio buddy Jan Willem.
HFA: While on the subject, can you tell a little bit more about the feedback?
Raphael: The local feedback is the feedback across the first stage of the amp, the voltage amplifier. Global feedback is across the whole of the amplifier, both voltage, and current stages, so from the inputs all the way to the speaker binding posts. What we do is to create a ratio between those two feedbacks from 0 to 100%, reducing one while increasing the other in 5 steps, where each step always gives you a total of 100 percent. In doing so, you change the damping factor but also other things like phase margin, but the gain is unchanged. When bi-amping, then you get something really cool because we can then change the feedback ratio independently for treble and bass. What we noticed so far is that people tend to leave the feedback for the treble at 0 percent to get a nice airiness, while the bass feedback is set a little higher to tighten the bass. It all depends on how you like your bass, and also on how the speaker is developed.
HFA: That sure is a fantastic option! On the subject of DAC, what type of conversion do you prefer?
Raphael: The C1 converter uses R2R ladder DAC. It’s an off-the-shelf PCM-1704 Texas Instruments chip, but we use 8 of those in parallel, meaning 4 per channel, in a balanced configuration, summing their current outputs. This way we’re counteracting, or rather, balancing the imperfections and tolerances that exist in these chips. Another thing we do is to calibrate these circuits to linearize them, thereby eliminating another set of imperfections of the IC. This process can be started via the C1’s setup menu and we recommend you do this every so often.
HFA: Truly very clever products!
Raphael: They’re Engineering-minded because we are engineers, and the components have got lots of little exciting gimmicks indeed. We did ask a female designer to do the casework design and we’re very pleased with the results. It’s much prettier than any of us Engineers could have come up with. The products now have a soft kind of touch which we think is more appealing to people.
HFA: Raising the WAF is a smart thing to do! What’s the reason for not going with Delta/Sigma?
Raphael: It’s quite simple: on this occasion, we found that R2R gave us better results. What we could bring on top of the chip itself, by calibrating and linearizing, would be much more profitable in R2R than it would be in Delta/Sigma. We do use Delta/Sigma on the analog outputs of our CD player, which is actually a Transport with digital outputs, as well as a built-in DAC and we also use Delta/Sigma in our integrated amp.
HFA: Is that cost-driven?
Raphael: No, not cost. We thought that the integrated amp could be good with Delta/Sigma. What we have is a very specific power supply to drive the reference of that Delta/Sigma converter. As I mentioned, there are no Op-Amps in our signal paths. But around them, there are tons of them because that’s where we think that Op-Amps can give you a real benefit for regulation, where we use them in shunt mode.
HFA: Which CD transport is used in the player?
Raphael: We use an Esoteric VMK-5 with a few tweaks on it. It’s a great transport that unfortunately is no longer available. But we have stocked up properly and have enough for a long time to come.
I also want to explain a bit about the CH Control app. It’s an attempt at decomplexifying the equipment and the way you access it with all the parameters. What you want is everything under one roof, so from day one, all our pieces of equipment have got an Ethernet port. All these devices can be controlled from an App, wirelessly, via the normal wifi router. The CH Control App lists all the connected CH Precision devices, with 2, 3 or 4 tabs for each device, among which are status and settings and the latter shows all the available settings that can be made for that piece of equipment. These can be audio-related things or cosmetic things. For example, you can rename or leave out inputs and change the color and brightness and gamma etcetera of the text on the equipment’s displays. Typically the amp has a power meter but you can also have the status or temperature. There are tons of other gimmicks that you can do. Or you can simply have it off. This is a great help for people, being able to adjust all this from the comfort of the listening position. And, of course, the usual things that an infrared remote control would do, such as volume, phase, and input selection, are also available. And all devices can be switched on and off from the app.
HFA: This is an Android App. Is iOS on the radar?
Raphael: I won’t say “never”, but not at the moment. The thing is that Android is more stable than iOS in terms of how often it changes dramatically, requiring App developers to also implement changes. An iOS update might actually stop an App from functioning properly. Another thing is that we are a small company. We have a software developer that does the App, but this is not his only job. If you have two Apps to maintain all the time, and on top of this having to implement changes in response to changes in OS, well, then you spend your life doing it and we can’t afford that. That’s why we had to choose for Android. The streaming input supports all sorts of formats: WAV, FLAC, DSD, DXD, etcetera, it’s pretty universal in that sense. By the way, we’ve got two new things coming for the App: Tidal and Qobuz.
HFA: Do you know of a reason why Music Servers also differ in sound?
Raphael: I think the collective answer from the entire industry is that we don’t really know. Nobody knows exactly. Think back to when CD was first introduced. Audiophiles agreed that it didn’t sound very good in the beginning, but look how far we came and it’s pretty decent now. I think we will see a similar process for servers and streamers. There are just a few more things that collectively we have to do. We just have to eliminate layer for layer, what is causing the problem, and this takes time. We provide the receiver, the Renderer, and people can do what they like on the source side. We do get a lot of feedback from our customers, which gives us clues.
HFA: Is the Network card RoonReady?
Raphael: Not at this moment in time. The trouble is that we are UPnP compatible but Roon is not, and they are not going to be. We do have some plans and have spoken with Roon and we think that we should become compatible at some point. Right now, the C1 works with Roon via USB.
HFA: Thank you very much, that was an incredible amount of very interesting information!
Raphael: You’re very welcome!
Update December 2022
In August 2021, Raphael went on to pursue another job career as an Electronics Teacher. CH has since appointed Kevin Wolff as a dedicated person for international sales.
The CH Precision team is composed of the following people
- Florian Cossy: CEO and founder of the company. The C in CH.
- Loris Stehle: mechanical and software design engineer
- Eduard Kohler: Software design engineer (app, low-level firmware, FPGA, DSP programming)
- Raphael Pasche: hardware design engineer (no longer with the company)
- Kevin Wolff: Head of International Sales
- Dino Jordao: head of Production, Procurement, Quality Control, etc. The list could go on forever, he is essential in making sure that what we make is perfect and goes out of the door on time.
- Andreia Jordao: production, final assembly of units
- Carlos Sa: production, final assembly of units
- Ana Rei: production, sub-assembly preparation
The co-founder of the company, Thierry Heeb (the H in CH), works for us as a contractor. He still owns shares in the company but doesn’t work here on a daily basis. His specialty is in DSP and FPGA audio programming (for example upsampling processes, filtering, etc).
More CH Precision
CH Precision C1+A1 Extensive Review
CH Precision A1.5 Extensive Review
CH Precision A1.5 compared to Soulution 711
CH Precision P1 Extensive Review
Hello,
According to you, what will be the best match CH Precision electronics with Apogee Duetta Sig ?
Thanks and regards,
Patrick
Hi Patrick, I’ve not heard the M1.1 but have owned the A1 and the A1.5 and can tell you that the latter works with the Duettas absolutely superbly. If you’re on a budget then a second-hand A1 is also a good option, providing a super-detailed yet extremely refined performance that very few amplifiers will be able to match.
Dear mr. Punter,
Thank you for your distinctive reviews.
Question, do you already know more about the upcoming upgrade for C1 DAC later thuis year ?
I hope you will have the opportunity to upgrade your C1 DAC and plublish a review in the future.
Kind regards,
Fred
Hi Fred, all I know is that it is coming, that it is not a matter of swapping option boards but the main circuit board needs changing, and that the change in sound is said to be substantial. I don’t yet know if I will do the upgrade.