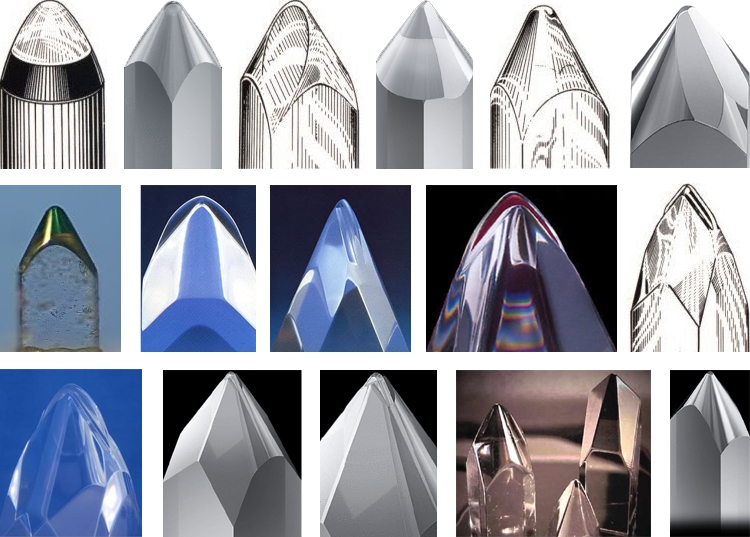
This article is born out of a desire for having a comprehensive source of all the relevant information pertaining to the various Phono Cartridge Stylus shapes, their differences, and overlap. While much of the info below can be found elsewhere (after all, the techniques are all decades-old), it is scattered all over the internet. Thus, I decided to compile everything I know and all that I found into a single comprehensive article covering all the bases.
Besides my own accumulated knowledge, sources include cartridge manufacturer websites, Wiki pages, and several fora. Especially noteworthy are the VinylEngine and Lencoheaven fora.
All of the familiar Stylus Shapes will be discussed in detail below. Further, I will explain the aspect of Contact Area, Bonded versus Nude diamonds, and the difference between a Round Shank and a Square Shank.
Familiar Stylus Shapes
Conical / Spherical
Elliptical
Line Contact / Linear Contact / Special Line Contact / Fine Line
Shibata
MicroRidge / MicroLine
Jico SAS
Exotic shapes
There are a couple of exotic shapes intended for the real connoisseurs that I will include for completeness but that, so far, I have no personal experience with and will not discuss for now.
A.J. van den Hul
Fritz Gyger
Paratrace
Stylus Shapes
Conical / Spherical
The cross-section of a Conical/Spherical stylus is a perfect round circle, as illustrated below.
The simplest of stylus shapes, easy to make and cheap to buy. While this shape can lead to highly engaging and subjectively musical results and often with remarkably powerful bass, this shape does not trace very precisely. The spherical tip only touches the center of the record groove walls and its broad (large) contact area prevents it from making detailed contact with the fine modulations inside the groove walls leading to lower fidelity. Lower resolution and spitty S’ses aside, new records will still fare relatively well but especially older and more worn vinyl won’t sound very good with this kind of stylus.
Conicals statistically trace less of the surface area of the groove wall, so they can theoretically pick up less record damage (unless they trace an area where there HAS been lots of wear or damage) and can pick up fewer sonic bursts from defects or noise from dirt or other foreign objects in the groove. But the wear factor is much higher for both the record and stylus.
Denon DL103 is probably the best-known cartridge that uses this stylus shape and its popularity shows that not all music lovers are in search of the most detailed sound.
Elliptical
The cross-section of an Elliptical stylus is an Ellipse, which is a flattened circle, created by taking a Conical shape and shaving slivers off the front and rear, as illustrated below.
Invented in 1970 and patented by Grado, the Elliptical stylus, in its most basic form, is a Conical stylus with slivers shaved off on the front- and rear sides to make for slightly narrower contact surfaces on the sides. The better Elliptical styluses (for instance Hyper-Ellipticals) are made with higher precision and are often closer to a Line Contact shape.
Any Elliptical stylus has two different radiuses – a larger diameter at the sides and a smaller diameter front-to-back. The larger front radius rides in the center of the groove just like a conical stylus, while the smaller side radius has a narrower contact with the groove walls. While a relatively simple measure, this results in considerably more accurate tracking than with a Conical-shaped stylus. Especially “Special Elliptical” types can lead to wonderful results.
Line Contact / Linear Contact / Special Line Contact / Fine Line
The cross-section of a Line Contact stylus can be regarded as an Ellipse taken to the extreme and with straight vertical edges (rather than round) for deeper groove contact, as illustrated below.
The Line Contact stylus shape can be considered a later variation of the Stereohedron stylus (with its four slivers shaved off, it is sort of a double elliptical) as patented originally by Pickering in 1973.
Patented in 1978 in Japan by inventor Junshiro Ogura, the Line Contact stylus is shaped such that it allows maximum vertical contact with the groove walls whilst having a small front-to-back contact. This kind of stylus is almost always fitted with a nude diamond. Compared to Conical Styluses (that due to their rounded shape only touch the groove walls in one vertical spot, thus more easily wearing them out on that depth), Line Contact styluses can make slightly worn records (when worn as a result of the use with conical or elliptical styluses) sound almost pristine. This is because the larger vertical area can now be modulated by previously untouched areas of the groove walls.
The variations such as Linear Contact, Special Line Contact, and Fine Line all represent further refinements of the principle, usually adjusting the shape of the shank and/or the width of the contact area. The variations with the narrowest contact area such as Ortofon’s Fine Line, Audio Technica’s Line Contact, and the more generic Special Line Contact achieve the most accurate results with the best high-frequency response and lowest distortion. All the variations have in common that the stylus wears more evenly which results in a longer stylus life.
In general, the more precise the stylus shape, obviously, the better it is at picking up high frequencies but also the better it is at picking up small defects in the pressing or very brief noise spikes. Compared to the simple Stylus shapes, the Line Contact and more advanced designs require records that are cleaner and in better condition to be played mainly noise-free. But in my book a little playback noise here and there certainly does not stand in the way of my musical enjoyment, and even if so, usually, it’s nothing a record cleaning machine can’t fix.
Shibata
The cross-section of a Shibata stylus is basically an Elliptical shape with extra slivers shaved off on one end to create a hybrid asymmetrical shape, as illustrated below.
Invented by Mr. Shibata and patented and assigned to Victor Company of Japan (JVC) in 1973, the Shibata shape is part of the Line Contact family and originally developed to accurately track the high-frequency information (up to 45kHz) on quadraphonic records without wearing them out, the Shibata stylus has two radii, similar to an elliptical stylus. However, the Shibata has a more complex asymmetrical stylus shape that is cut to form a line contact while also allowing more surface contact.
Through better groove wall contact the tracking and information retrieval are improved, resulting in a better than before HF response, and because the total contact surface area is increased, the amount of pressure per square area is substantially reduced, resulting in less wear on both the record and the stylus.
Playing back a record with a Shibata stylus which has been worn with a conical or elliptical stylus can produce near-perfect playback. This is because the Shibata shape (as do the more complex shapes discussed below and, to varying extent, also the Line Contact shape) reaches areas of the groove wall that were not contacted by the simpler stylus shapes.
MicroRidge / MicroLine / Microlinear
The MicroRidge cross-section is very complex but probably best described as a mini Philips screwdriver shape, as illustrated below.
Although I won’t include detailed information on any of the exotic stylus shapes, it’s worth noting that A.J. van den Hul of the Netherlands actually pioneered the use of advanced computer analysis to create laser-cut shapes with the “Van Den Hul stylus” that was patented in 1978. The patent abstract reads “The tracking edge of the taper is V-shaped and has a rounded tip. The two ground sections which form this edge are symmetrical and run convex for optimum playback”. Juicy detail: van den Hul claims that Namiki later manufactured his design without paying royalties.
In any event, it was the van den Hul design that inspired the shapes that I will discuss next.
Patented by Namiki of Japan in 1983, the MicroRidge is a very complex shape that has been made possible only by using laser-cutting techniques. The MicroRidge stylus almost exactly duplicates the shape of the cutting stylus that produces the original master disc at the vinyl pressing plant.
On the surface, the shaft shape is similar to a Line Contact stylus but if you look closer and zoom in on the very tip of the stylus, you’ll notice the tiny ridges of only a few microns which are the only point of contact. The MicroRidge stylus is shaped to allow the narrowest possible horizontal contact area. The radius of the vertical contact area may differ from brand to brand but, in general, MicroRidge styluses maintain a similarly large vertical contact area as the Line Contact stylus. The MicroRidge shape also wears more evenly, greatly extending record and stylus life.
MicroRidge styluses provide more accurate tracking than all the above variants with even more detailed high-frequency retrieval and again considerably lower distortion than even a Shibata or Fine Line stylus. I have not yet used any of the exotic shapes such as van den Hul, Gyger, or Paratrace but of the ones that I did use, MicroRidge is by far my favorite. However, cartridges with this stylus shape do require a very careful setup. After all, it is easier to align a rounded end to a groove than a V-shaped end.
Some listeners may perceive a MicroRidge stylus’s cleaner and more accurate bass as relatively thinner. Sometimes this is indeed the case (AT150mlx springs to mind) but it’s also a relative and perceptual matter. It’s actually more likely that the simpler stylus shape that a Line Contact stylus is compared to actually has overblown bass. Also, a lean bass can be the result of incorrect alignment. The smaller the contact area, the more important it is to have the stylus positioned in the groove at the precise SRA (rake angle)/Vertical Tracking Angle (VTA) and, even more importantly, with perfect Azimuth. Especially the latter aspect can be more difficult to get just right and require more patience than with the simpler stylus designs.
Variations on this design are the Audio Technica MicroLine, Shure MicroRidge, Dynavector, and JICO SAS. According to Bebé Tonto who dove deeply into spec comparisons and posted his findings on the VinylEngine forum, the minor/major radius dimensions and footprint for the Audio Technica MicroLine are exactly the same as Jico’s (Namiki’s) SAS stylus, leading him to believe that they are exactly the same stylus, both made by Namiki. Furthermore, the SAS stylus cannot be purchased for any of the current Audio Technica cartridges which further indicates a potential conflict of interest.
Jico SAS
Just like the MicroRidge shape, the cross-section of a SAS stylus is very complex and probably best described as a mini Philips screwdriver shape, as illustrated below.
SAS is a variation on the MicroRidge stylus created and marketed by the Japanese company Jico. There are those who suspect that this stylus is actually supplied by Namiki, see the MicroRidge section above. Interestingly, when viewed under a microscope, this shape looks somewhat similar to a Philips screwdriver but, of course, infinitely smaller. With the naked eye, one cannot see the architectural marvel that the SAS is.
So far, my experience with the Jico SAS shape has been limited to a replacement T4P stylus for a Technics MM cartridge inside the SL7 and SL10 turntables. While it was immediately clear that the SAS tracks significantly more accurately than any of the other styluses that I tried, I felt that its high accuracy also lead to a drier and leaner sound that instilled less of a “boogie” feeling in me. At the time, I also used the best Elliptical stylus that I could find: the one that was also made by Jico. In comparison, the latter provided beefier bass and a fuller, sweeter sound. The Jico Elliptical stylus’ treble was better than that of all other Elliptical styluses but the SAS clearly beat it in this regard, especially with slightly worn records.
As surprisingly good as the SL7 and SL10 turntables are (and they really are much better than most give them credit for), they remain “hifi” turntables, rather than “high-end”. Thus, the above results are far from conclusive.
I have yet to conduct a comparison with an SME-mount Jico cartridge but I suspect that it will lead to similar results as the MicroRidge styluses.
Contact Area
As a rule of thumb, the longer the vertical (top to bottom) contact surface, the better. This is illustrated by the two images above. While the right image shows a Line Contact stylus shape, the same is true for the more advanced shapes such as MicroRidge and SAS and, in a smaller part, also for Elliptical shapes. Below is a photo made through a microscope of a Conical stylus and a Shibata stylus in an actual groove.
The vertical groove wall surface is only one of two contact areas, though. There is also the aspect of the front-to-back contact area (illustrated below). Generally, the smaller the front-to-back contact area, the more accurate a stylus can retrieve the information in the grooves, particularly the high frequencies.
While there are various other important parameters, these are the two main differentiators among the various stylus shapes. The details of these two aspects and more can be read below in the respective Stylus Shape sections.
Bonded versus Nude
In a bonded stylus, a diamond tip is glued onto a shank of a different material (usually steel) that is itself glued onto the cantilever. While a bonded stylus saves a lot of diamond material and thus is less expensive to manufacture, this construction has a higher combined mass that can negatively affect the transient response. Nude styli, shaped entirely from diamond material, are more costly than bonded styli but their lower mass allows them to track more accurately. Generally, bonded styli are only applied in cost-effective styluses and cartridges and Nude is pretty much the standard for high-quality styluses.
Until 1977, diamond stylus tips used to be made from actual, natural, diamonds. After that, the industrial diamond made its entrance. Made in a lab and chemically identical in structure, artificial diamond is nevertheless said to be slightly less durable than real diamond.
Round Shank versus Square Shank
The stylus shank is the vertical piece that connects the needle tip to a round hole in the cantilever. A round shank is the simplest form and it is most commonly used in entry-level to medium-cost cartridges. The round shape can be more difficult to align precisely when it is affixed to the cantilever and this can lead to needle tip misalignment. This is a real factor and something to take into account when adjusting the cartridge in the headshell. A dead-on, straight-looking cartridge does not guarantee that the cantilever or stylus are positioned accordingly.
Square shank styli cost more to make than round shank styli, but they allow precise alignment in the case when they are mounted in a laser-cut square in the cantilever. Also, the square shape can lead to mass reduction.
Do note that while square shanks lead to a potentially more precise alignment, there can still be slight variations in all of the stylus’s parameters from sample to sample, even among same brand and same type cartridges. Thus, even with square-shank styluses, it remains advisable for all cartridges to use a test record and measurement software or a scope for precise alignment.
Longevity
How long does a stylus last? Unfortunately, there is no definitive answer to this question. Nagaoka quote 150-200 hours before damage to the grooves sets in for their elliptical styluses. Ortofon states that their affordable DJ-style “bonded” type diamonds reach about 600-1000 hours of stylus life while HiFi cartridges with Nude diamonds are expected to far exceed 2,000 hours with proper care and maintenance. Meanwhile, some of the very exotic brands quote even higher numbers.
What Ortofon also mentions is that another consideration to be made is that any diamond stylus will begin to exhibit physical changes after approximately 1,000 hours. This can lead to audible results.
An audio buddy with over 40 years of analog experience tells me that he got 1500-1800 hours from the Ortofon A90 MC cartridge that has the mythical Replicant 100 stylus and 2500-3000 hours from the Lyra Kleos with a variable radius line contact while indicating that Allaerts claims their styluses last 5000 hours. Of course, it all hangs together with use and countless other variables.
Different stylus shapes, materials, and sizes, as well as their contact area, alignment, and tracking force all greatly affect longevity and it is also important to note that these manufacturer quotes are for a given set of conditions. In general, though, the Line Contact and more complex shapes tend to last considerably longer than the Elliptical and simpler shapes.
An interesting aspect to keep in mind is that styluses may last for very long, but at some point prior to their maximum life span, they will start to damage the groove walls. How to prevent this? You can check your stylus with a microscope but you’d have to know what to look for (hint: it’s not the sharpness of the stylus point) or you could listen very carefully. When transients get softened and you find you need to raise the volume to create an artificial sense of dynamics then it may be time to renew the stylus.
Michael Fremer mentions the following in a Vinylengine forum (courtesy of member atomlow):
“I think you can safely play a stylus -any stylus- for at least 1000 hours assuming two things: you keep it clean by dusting off every side with at least a brush and that every few days at least you use a liquid or gel type cleaner, assuming the manufacturer recommends it. Today’s (more advanced) styli wear by softening the ridges or edges. In other words, the severe stylus profiles get rounded. Thus worn styli do not ruin records. So while the sound may somewhat soften and deteriorate (as a result of stylus wear) I don’t believe record wear or ruined records result.”
To sum up: if you want to extract the maximum longevity from your stylus, then always make sure to set it to the correct tracking force (as a mistracking stylus will cause damage, even when it is set too lightly), clean it after each LP side, don’t let it ride in the end groove for too long (where diamond dust will grate at the stylus), and keep your LP’s clean. Also, it is important to keep in mind that more costly stylus shapes from the Line Contact and up do pay off in terms of less groove wear. This is because their larger surface contact divides the pressure over the groove wall vertically.
More to come…
When I find the time, I will create separate articles to cover the differences between MM (Moving Magnet), MI (Moving Iron), and MC (Moving Coil) cartridges, explain all about the various Adjustment Procedures both by ear and via measurements, and more.
This is the best explanation/description of stylus shapes and pictures and sound quality and record wear that I’ve seen. Maybe when you have some time, you could add those exotic shapes? 🙂 A.J. van den Hul, Fritz Gyger, Paratrace. I suspect they are just small variations of the common shapes, to possibly allow for copyrighting. Thanks!!
The Paratrace is a Van den Hul but marketed by Expert Stylus UK under license as they produce for vdH.
can you explain how to possibly tell quality of diamonds, or where they are from?
maybe something on color of diamonds: e.g. should naked diamond be clear looking, or can it be black (like industrial)… Its hard to tell what quality you’re getting from which company/country.
Thanks, mike in SC
Forgot to thank you: i agree with above first post, this is the best summary I’ve seen in one place regarding stylus types/shapes/operation!
Thanks for writing this! Excellent!
mike in SC
Thanks:-)
Good question! The only information I can add is that if you look at the stylus via a binocular or microscope and it’s clear, bright white, and the flat edges refract light, the diamond is likely made of an actual gem. If the stylus is black or frosted, it is likely an industrial-grade diamond.
Thank you so much for this comprehensive and in-depth illustration of the theme.
Due to your knowledge, I would like to ask you a question.
Some time ago I bought a nos ortofon vms 30mkII. Due to extensive use of an Ortofon 540, I mounted that cartridge. I have taken care to make some minimal mods. I glued on the lateral metal body two pieces of wood with the appropriate shape to reduce the resonances of the shell. I can guarantee the audibility of the metallic resonances of the shell.
Good. I can say it sounds good. But probably due to the age and possible hardening of the elastomer, I prefer to read vinyl with two grams. Is this a good guess?
Thank for your attention.
Regards.
Girolamo
I’m afraid there is no universal truth when it comes to cartridge cantilever suspension aging. Sometimes, they stiffen up, sometimes they become loose, and sometimes, they don’t seem all that affected by the years. The best advice that I can give is to start with the recommended VTF (or a little less since your wood pieces have made the cart a little heavier) and then try it a little lighter and a little heavier. Just trust your ears. Too light and the sound lacks body and drive and you start to hear mistracking, especially with 12″ or otherwise very dynamic records. Too heavy and you lose pacing and liveliness.
good news. tracking is getting better with the use. I think that the ortofon suspension don’t suffer the age👍
Ok. Thank you si much for the rapid and util replie
Can you please add an explanation of how a tie-wire or stabilizer-wire can improve the tracking ability of a cartridge. It seems like that many people are unaware that their sub-$50 styluses are lacking this crucial feature.
How can the elliptical stylus be “Invented in 1970 and patented by Grado” when Shure was selling these in 1964 with the introduction of the M55e and V15 type-I cartridge?
To make sure, I looked up the patent and it turns out a ROBERT B. PULESTON is named the inventor. This patent was filed in 1970 and Grado is also mentioned in it. The Patent document can be read here. Not sure what’s the deal with the Shure stylii you mention that claim to be Elliptical. Perhaps it’s just a legal matter, the method being invented by more than one person but only patented by this particular person/entity.
Been at this game for over 40 years, lots of Cartridges and tables along the way. Have to agree this is a great summary of part of the best thing audio
has to offer. Cartridges, Tonearms and Turntables matched well sound magical. The combinations are endless, it never gets old. Thanks 🙏
Thanks for the comprehensive explanation on stylus shape. Which impact has the stylus shape on anti skating settings? Most turntables only show values for conical and elliptical stylus (if at all). Do MicroLine/MicroRidge need more or less anti skating? Thanks for your advice.
In my book, it remains a matter of trial and error. Simply listen for distortion/sibilance in one channel (and make sure it is consistent in several records, not just the one) and adjust the anti-skating accordingly until the distortion is gone or reduced or at least equal between the channels.
It confuses me that Special Line Contact is mid-level in your hierarchy and Micro Ridge is at the top, yet Audio Technica say their Special Line Contact is their top stylus and Micro Line more mid level (below Shibata). Eg OC9XSL and OC9XML (the latter having the same Special Line Contact stylus/cantilever as the ART1000).
If Audio Technica is right, that makes your article confusing to me.
That’s Marketing I guess:-) For instance, Micro Line was always top of the bill (officially still is) but now that it is scarce, Shibata is marketed as better or best. I bet a similar mechanism or word-play is at work here.
Also cots incurred through licencing, for instance Namiki Microline is technically superior but costs less to use than Shibata
The very best summary about that topic I found so far. Thanks a lot !
Good artice, interesting and well written. Just wondered where vivid line stylus sit in the rankings as sold by lp tunes.
Glad you enjoy the article! I am not familiar with Vivid Line but from doing some searching in Google, it seems it is a marketing term for a hyperelliptical shape (finer than standard elliptical).
Excellent overview and easy to follow. I learned a lot and this helped me in narrowing down what I should look for when soon choosing my next stylus. I look forward to the next article on pick-up types their pros and cons.
Thanks for a really interesting & well written article. As you already know, it’s not easy to find such a summary anywhere and I was becoming frustrated by my lack of understanding of the various types of stylii, at the same time my awareness of different cartridges increased. Your piece has solved that problem!
This is outstanding!!! Thank you so much for taking the time to do this.
good article and explanations .very informative.vinyl has made a comeback to a degree.articles like this keeps us interested in the vinyl format.
Thank you ! The best deep-dive rabbit hole on multiple aspects of the subject bar none!
Wow, thank you for this indepth explanation! I really appreciate you taking the time and effort to educate me and others on such an overlooked contribution to our audio enjoyment!
Again, thank you!
Thank you for your exceptionally clear and truly fantastic explanation of the different stylus shapes. This is exactly the information I have been searching for for quite some time! Thank you!
Thank you very much for these great explanations. As owner of several Pickering Stereohedron styli I’m wondering where to put them on the ranking?
Hi Peter, I do not have any personal experience with Pickering cartridges, but from what I can find online, it looks like it has common features with the Shibata stylus. Here’s a bit of information from the manufacturer that I found: “Like its cousin, the Quadrahedral, the STEREOHEDRON stylus is shaped to provide an enlarged area of record groove contact, while providing the ability to accurately trace the high frequency, the level modulations found on today’s records”
Appreciate for your efforts to gather and summarize the information with detailed explanations. I didnt know any of these when I ever played Vinyl records in mid 80s. Would love to see deep dive topics about the cartridges, choices of cartridges and how to match the tonearm to the cartridge if there are specific requirement.
Great work bringing this information to one article.
Should note that the Ortofon Replicant is a Fritx Gyger S, possibly poished or graded to 100 /110/120 spec but all made by Gyger in Switzerland same cut as their 5/120.
Paratrace is made at Expert Stylus who (Wyndham Hodgson) also produce for Van den Hul.
If you want a story of intrigue look up the Van den Hul & Fritz Gyger story.
There were only 3 or 4 outfits making stylus tips a few years back, this may have changed with the Chinese entering the market.
The major players were Fritz Gyger AG, Ogura & Namiki. All the big cartridge manufacturers used their diamonds, but often obscured the details and used exotic names to market.
For instance look at the Denon DL110 and compare it to the Ortofon OM-30, under a microscope they appear near identical with the same greenish tinge. The Denon is called a “Special Elliptical” while the the Ortofon is a “Line Contact” both are 8/40 uM.