Technics Linear Tracking Turntables – part 1
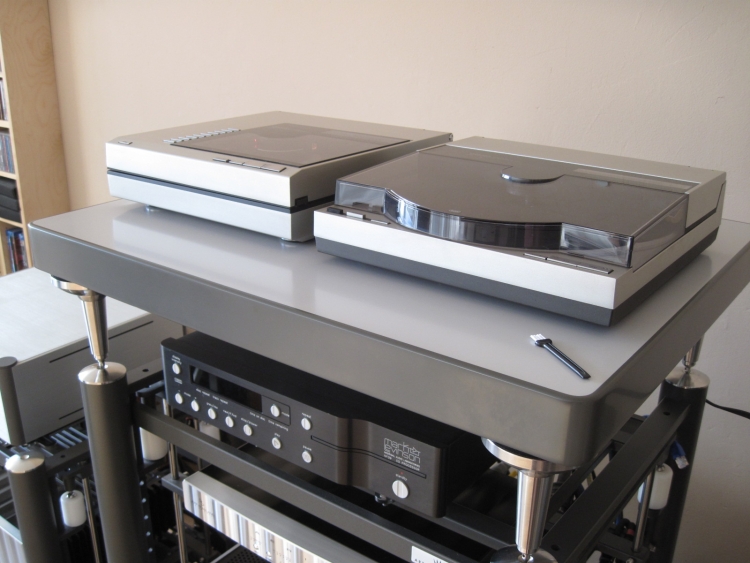
The analog audio bug has bitten me again…
In order to further assess the Artesania Turntable Platforms that were over for a review, a friend brought over a humble Technics J3, just for the fun of it. Interestingly, this cheap plastic unit managed to sound emotionally utterly engaging, communicating in a manner that even my best CD players failed to do.
And so, I was once again bitten by the analog audio bug.
Avid Volvere turntable, Grado and Benz cartridges and Musical Fidelity M1 Vinl phono stage kindly supplied by StudioAlkmaar
On the main picture and above: the best Technics linear trackers: SL15 on the left and SL7 on the right. But let me tell you all about how this story started.
First: a disclaimer:
The turntables reviewed here are 30+ years old. It is not uncommon for turntables of this age to have worn bearings or, especially in case of linear trackers, aged electronics causing misalignment of the arm. While I found no evidence of the former, I did encounter the latter, but I compensated for this by carefully re-aligning the servo settings. Nevertheless, I can’t rule out that some of the conclusions that I reach are clouded or influenced by the mere age of these players. That said: they all sound wonderful, and especially after recalibration, it seems that they perform just perfect.
Let’s start the show
It all started with the humble J3. On top of the superb Artesania Krion turntable platform, which is large enough to hold two Technics linear trackers at once – very handy for my comparisons!
After the positive initial experience with the J3, I decided to purchase a Technics SL-7 for myself. 35 or so years old, and still going strong. The SL-7’s top part (body and lid) is made of aluminium diecast and its bottom part (the dark grey bit) of zinc diecast. Given its diminutive size, the SL7 seemingly weighs a ton. As you can tell from the above picture, they use completely different mechanisms as well.
J3 and SL-7
98% plastic J3 on the left, 98% aluminium/zinc diecast SL-7 on the right – just kidding with those figures of course, but despite being built from different materials and having different automation- and arm mechanisms, the J3 also has some things in common with the SL7, which is something that can’t be said about the SL10 and SL15.
One thing that surprised me was that the platter motor mechanism is seemingly the same for the J3 and SL7.
Above: the stator part of the direct drive motor for the J3
Above: the rotor part of the direct drive motor for the J3
Above: stator part of the direct drive motor for the SL-7 – notice the similarity? All the plastic of the J3 is now aluminium and zinc diecast, but the SL-7 platter motor, while not a 100% copy, follows the exact same principle as in the J3. This is actually a much-reduced version compared to what’s in the SL10 and SL15, as we will see later.
Above: rotor part of the direct drive motor for the SL-7. The Magnet assembly is identical as far as I can see.
Above: the SL-7 platter, however, is thicker at the edges, and quite a bit heavier.
Tangential Tracking Principle
The tangential principle for all the Technics variants remains the same: a servo controlled worm wheel connected to a radio-dial-reminiscent rope that pulls the arm assembly. This is activated via an optical sensor upon dis-alignment of the arm as it is pulled toward the centre of the LP.
The whole arm assembly rests on a lubricated metal rod. Supposedly, this type of linear tracker manages to retain an amazing 0.1% tracking angle error. Well, that number sounds very good to me at least, but I’m not (yet) a vinyl expert and I honestly don’t know what tracking error percentages normal record spinners yield.
btw Cartridge shown in these J3 pictures is the standard EPC-P33 with a cheap replica stylus. We swapped it out for an EPC-P540 with original 540 stylus and it made a very, very large difference to the sound: much more refined treble, more low-level detail and more air with less ragged edges. The P33 had already been fitted with a brand new stylus but clearly, that didn’t help cover up that the cartridge can be bettered. The EPC-P540 did have less forceful bass though.
It may well be that normal pivoting arms cannot manage such low tracking error percentages as the Technics linear trackers, except on two places on the record. At least audibly I can attest to the fact that typically the last tracks on LPs sound worst. I’ve heard it countless times in friends’ setups as well as my own, when I still owned a Michell Gyro SE. Guess what? The Technics linear trackers sound as distortion-free on the last track as they do on any other track on the LP. And what’s more: I don’t hear any off-centre-related speed variations.
The downsides? Two that I know of. Supposedly these more complex systems are prone to break down. Well, all the linear Technics units I’ve seen, still play on nicely after 35 years. Second, you’re supposed to be able to hear the servo as it pulls the arm in short bursts every 2 grooves or so. Well, I don’t hear anything there either. Direct drive related downsides? Again, I don’t hear them. But I do hear the upside of Quartz lock though: perfect pitch and superb transients.
But I’ve only got MM cartridges to play with. The story might be different with the more sensitive MC variants. After all, the signal is much weaker and needs to be amplified more, and in the process, more rumble might be picked up. I don’t know. And I don’t really care. They are just too much fun.
SL-7
In the SL7, the arm assembly is built right into the cast aluminium lid, as opposed to being built into a separate folded metal part in the J3. Contrary to what is said on the Vintage Knob site (“The SL-7 is an SL-10 sans built-in MC preamplifier, with less aluminium and more plexiglass”), the SL7 has very little in common with the SL10 and SL15. The Vintage Knob is right in that the SL7 lacks a MC to MM preamp, but otherwise, the info is wrong. SL10 and SL15 are actually practically the same machines, but the SL7 stands out.
Compared to the earlier SL10 and SL15, the later SL7 has completely revised electronics, a simpler platter motor and a different arm mechanism. The latter still works via motor-worm-wheel-waxed-rope, but the plastic assembly covering the rope is very different. The arm itself is also slightly different, as is the locking mechanism. Oh, and the SL10 and SL15 have a mostly metal puck, while the SL7 has one entirely made out of plastic. The SL7 and SL10 also sound very different. “Oh dear, there he goes again”, some readers might think. Yes: I’m saying that I hear clear differences between SL10/15 and SL7 using the same cartridge and styles, and the same 1.4-gram tracking force (needle pressure).
btw: Technics recommends 1.0 – 1.5 grams, aiming for a centred 1.25 grams. Importantly and conveniently, all T4P cartridges and stylii are made to this spec. Even so, I found that it is good to check the actual tracking force with a digital meter and adjust accordingly, not only relying on the mechanical indicator.
Initially, I noticed that 1.4 is just right: 1.5 makes for better bass but kind of suffocates dynamics and fluidity. Lower settings improve fluidity and air but at the cost of bass power. For the remainder of part 1 of this review (this page), I used all Technics T4P turntables with a calibrated 1.4 grams tracking force. However, recently I found out that the EPC-540 cartridge in the SL-7 was slightly loose and I tightened it, without giving it another thought. When I had a friend over a few days later and we listened to the SL-7, I found that it sounded a bit restrained and too controlled. It then occurred to me that my preference for a higher than usual tracking force may have sounded better only because the cartridge was not fixed in place well enough. I recalibrated to 1.25 grams and yes indeed: back was the fluidity and agility. So, from this point forward (next page of this review) I calibrated all Technics players to 1.25 grams.
For best tracking, as well as lowest wear, some believe that tracking force better be nearer to the highest value that the manufacturer recommends, while others believe that it can better be set nearer to the lowest. Opinions on this matter differ, and even the experts can’t seem to agree, so I suggest you experience for yourself and form your own opinion.
Tracking Force (Needle Pressure)
How did I manage to measure tracking force with these Technics players? It’s a bit tricky actually because they’re made to be foolproof. They won’t lower the arm unless there’s a record on, and not unless the platter is spinning. Here’s how I do it. First I trick the player into thinking the lid is closed by pressing the contact switch, then move the arm to the middle position and switching off power so that it stays there. Unfortunately, it is really, really dummy proof and it raises the arm again right after switching off the power.
Ultimately I found a way to jig the arm lowering mechanism, simply by blocking the lever that takes it up again. I then place a digital needle pressure reader in the right spot and carefully lower the lid.
Oh, it looks like if one really wanted, the counter weight’s position could probably be changed slightly, further enabling tweaking (negating) the spring’s tension.
That’s an original Technics EPC-P540 in the SL7: a big improvement over an EPC-P202 which itself seemed to be an improvement over the P24, but perhaps my particular P24 was not in optimum shape, as apparently all the Technics P-mount bodies are the same. There’s a scale indicator for the needle pressure near the adjustment screw all the way at the back of the top cover, under the arm, but it’s not very precise. It’s supposed to be at 1.5 grams in the middle position, but I already measured enormous differences between the various players when set to that middle position. The screw tensions a spring that adds pressure to the metal weight that is at the end of the arm. This is how these turntables are able to play vertically. However: too much spring tension can have a dynamics crushing effect (Thorens owners take note). That’s why I like to keep it slightly under the recommended 1.5 grams.
Sound – J3 versus SL7
The big difference in sound between the J3 and SL7 is in timbre/tonality and dynamic behaviour. While the J3 is very lively and engaging and has a beautifully open midrange and treble, it is also devoid of colour and sounds a bit synthetic. Pianos sound more like keyboards. And bass, while fast and articulate, is less than full-bodied. The J7 sounds much fuller, yet less coloured. It’s almost as if you can hear the calming effect of using lots of aluminium/mass. However, the SL7 sounds dynamically more compressed: all sounds being seemingly equally loud.. Not good. Setting the needle pressure to 1.4 grams helps, but not enough.
Next suspect item was the clamp. While it may look loose and wobbly when touching it hanging from the lid, it actually contains a spring and is pressed tightly to the record when the lid is closed. That’s the other reason why these players can play vertically. But I remember from earlier turntable days that clamps, especially heavy ones, do more damage than good. They improve sonority and calmness but, you guessed it, they crush the dynamics. The player still sounds fast (it doesn’t have pre-ringing, like a CD player) but still it’s like the transients are stopped in their tracks before reaching full potential, in a word: they sound topped off. Removing the SL7 clamp is not very difficult, but it requires unscrewing a lot of screws, and careful removing of the plastic part of the lid. With the SL10 it’s a little bit more fiddly as it requires the removal of the plastic inside cover that can’t easily be totally removed.
With the clamp removed and used with the same EPC-P540 cartridge in the J3 and SL7, the SL7 now sounds just as fast and dynamic as the J3, but with much fuller tonality and no synthetic feeling whatsoever. For fun, I momentarily placed the puck back on the record manually, without the spring, but even that has an influence on the sound, and I don’t like it.
SL-15
The same owner of the J3 then brought along an SL-15. Turns out he has a whole fleet of these preciousnesses. The J15 is the big brother of the J10 and it is built almost exactly the same. Obvious difference is the track programming section on top and this is actually very cool: the player scans the record and makes a distinction between the tracks which can then be programmed to play. Say you like only track 2 and 3 then just put on the record, close the lid, press the buttons 2 and 3 and off you go. Well, not always. Maybe the electronics are a little off, or not all records have clear enough distinction between the tracks, but it doesn’t always work. But never mind: the rest still works beautifully, and in playing the SL15 sounds a lot like the SL10. Please note though that the record clamping puck for the SL10 and SL15 is made mostly of metal as opposed to all plastic, and that this means that its negative influence on dynamics is even bigger than with the SL7. Because I don’t own the SL15, and the owner doesn’t want to have the puck removed, I will leave it aside for further comparisons.
Coming Up Next
In the next instalment of this review, I will directly compare the SL7 and SL10 with the same EPC-P540 MM cartridges, and I will see what the influence is of the Artesania platforms on which they sit. Also, I have obtained another SL10 with an original EPC-310-MC cartridge and I will discuss the benefits and downsides of MC versus MM by means of 2 different phono preamps: the Musical Fidelity M1 Vinl and the Jeff Rowland Cadence.
What’s more: I managed to borrow a beautiful Avid Volvere with SME 309 tonearm from Ben Hoedjes, proprietor of Studio Alkmaar, an audio store in Alkmaar Netherlands, that sells new and second hand high-end audio equipment.
The Avid Volvere will be compared directly with the best of the Technics direct drive crop. Will the Avid crush them? Or are the differences not all that large? All will be revealed in the next instalment!
Hey Chistiaan,
I have one problem with my sl7, perhaps you have a solution: I have a
few records that are very long and the sl7 lifts the arm before the end
of the final track. I’ve read of different standards (DIN and IEC)
concerning the inner radius of records…
Is there a way to adjust the endposition?
best regards
Sven
DIN and IEC are standards for adjusting pivot arms and have nothing to do with linear trackers. End position on the SL7 can be adjusted somewhat but this is a hard switch that should not work intermittently. Does it always lift at the same position? If so then you may need to adjust the position at which the microswitch is activated. This can be done by removing all the screws on the inside of the top panel and removing the black plastic part. If not, then I think your arm belt may be slipping, resulting in an increasing off axis angle of the arm toward the end of the record, which may trigger the uncue. Can you see if your arm is at a 90 degree angle across the entire record?
Great write up. Thank you
Wanted to add that on SL-10 the metal puck is modest 80g and the only thing that needs to be removed is the spring pushing it towards the platter
Indeed, only the spring needs to be removed:-)
Thanks for Your fast reply.
As I remember this problem occured also when the sl7 was new (in the 80ies). It only happened with a few records with a runtime of about 30’+ per side. All shorter records were played completly. At that time I thought it was a limitation of the tangential system (brought up in the 80ies without being suitable for some rare perhaps “bad” produced records from the 70ies) and not changable. The arm always followed the 90° angle across the entire record (besides its “dancing” when the hole of the record is excentric)
So if there is a microswitch, who’s position is adjustable, that sounds great.
Background is, that I want to reactivate the sl7 for digitalisation of my records to put them on hdd, to make them more accessible for the whole family as flac-files and in mp3-files for our various cars (some of them older than the sl7 with tapedecks that are worn out and require a small suitcase for the tapes : ) ). These decks shall be replaced by receivers (without any moving components) that are connected to the obligatory smartphones.
Do You have any recommendations before reactivation of the sl7 – that sits still for some years – , such as lubrication of the mechanic?
The original Technics P202C is still mounted. How does one check if the needle is worn out? Are there criteria to see this? Should it be cleaned (ultrasonic bath…)?
Is it possible to change the needle only? Or does the whole cartridge need to be replaced?
My alternativ to the sl7 would be a slightly older Telefunken S600 with a Sure V15
What kind of external usb-soundcard would You recommend for the digitalisation process? Does it make sense to make 24bit at 192 kHz files? Or will the 16bit at 41kHz of the CD be already oversufficient?
best regards
Sven
Hi Sven, there is a microswitch indeed, and although perhaps not meant to be adjusted by the user, the way that it is attached makes it possible to adjust this somewhat, hopefully enough for your situation. A lubrication may not be required but chances are that the little rubber belt that moves the arm is deformed and perhaps stretched. But even so it might not require service beyond some trial and error. I’ve seen situations where the belt was indeed deformed and slipping at first, but the turntable started working after a few tries, spread over a couple of days. The beauty of the way that the tangential system is implemented in these Technics decks is that there is an optical sensor that counts how much the motor is actually moving the wheel that moves the arm so even if the belt is slipping a little bit, the motor will just keep on turning until the intended amount of rotations is reached. The arm sensor itself drives this process and is ultimately responsible for keeping the arm at a 90 degree angle.
In my experience the 202 is one of the best cartridges you can get for this player, but do check the state of the needle. The cartridge can also be replaced but unless you buy something quite expensive (Ortofon still have some nice P-mount cartridges), there is not very much to gain here. You can just swap the needle and leave the cartridge in place. You cannot see if the needle is worn out and even experts with magnifiers need to really know what to look for. Replacements are not very expensive and if in doubt I would just get one. Please do not buy just any replacement because I found large variations in needle length between the various samples I tried. None of them were the same length as the original until I found the needles made by Jico. Note that the needle can never be at a perfect 90 degree angle if its length is off. The Jico needles are more expensive but track better and also sound better. SAS (approx 125 euro)is the best and retrieves most information but is also a little more analytical. The cheaper Jico needles (approx 50 euro I believe) look like ordinary ones such as those from Tonar, but have much better needle tips (and perhaps other shafts as well), and although they don’t reach the levels of detail of the more expensive SAS needles, they have a fuller, more forgiving sound.
Between the S600 and the SL7 this is up to you. Belt drive and direct drive are very different in sound from each other. Shure V15 is a very smooth and full sounding cartridge that can also sound very pleasing. I would advise to get the SL7 back up to speed and just compare the sound of the decks then decide for yourself. You can always leave the SL7 as is and do some records on the Telefunken if the SL7 quits too early on some records.
Using higher Sample rates and bit rates finally is something that does make a difference in terms of treble refinement and soundstage accuracy, but given your intended listening in the car, I wouldn’t worry about it and go with 44/16. In my opinion, a digital recording never truly captures the spirit of analog records anyway, no matter how highly you sample it.
Hey Christiaan,
with all Your kind input I went to work and plugged the sl7 to the mains and the phono in jacks of my Audiolab 8000A. Power on, the red LEDs are lighted but no reaction when pushing the start button, not a single noise or movement exept the LEDs of the start-button…would have been too easy…
Power off and dismantling of the plastic cover…taking off the rubberbelt from motor and wheel moving the tonearm: it was deformed in an egg-shape and the motor didn’t move at all, i couldn’t rotate it with my fingers in the built-in-position, so I took it out of it’s bracket… now the axle could be moved with quite an amount of force, I turned it left and right with my fingers quite a while until the forced needed got less, then I tricked the electronic and pressed “start”. It began to spin with significant vibrations…letting it spin for a while in all different angles (to let the lubricant disperse in all directions) the vibrations diminished and ceased finally. Back in place the arm moved like it should….fine.
Being so succesfull, my attention went to the microswitch, that is attached to a cut out sheet-metal plate. Near to the switch are slots to insert a screwdriver for slightly adjusting the position by bending the metal plate, at least that’s what I thought, until the part of the plate with the microswitch broke off from the rest of the plate… I was desperate…The material of the plate was very brittle and not ductile at all… I thought, it would be the end for that day, already imaginiging about manufacturing a repair-plate, having in mind that a total stripdown of the cover would be necessary to work on the plate…..arrrgh….
But fortunately hot-glue was invented… five minutes later the microswitch was in it’s new position….it’s more a soviet-style repair than high precision work, but it does its job. (if You whish, I could send some pix)
By the way: On the sliding-chassis of the arm is one plastic nose in which is an adjusting screw for the start position microswitch. For the end position microswitch there is only the plastic nose to touch it. Looking carefully at it, I discovered that the nose was manually treated. I remembered again, I had the sl7 to service for it’s not playing to the end of my long records… and I remembered, they couldn’t fix it…
The big surprise was, that there must be some other device/switch lifting the arm at the end of the record, because I positioned the broken off switch so far to the left, that the nose didn’t touch it at all but it was lifted before! I suppose, that the sliding-chassis may be blocked by the limitation of the rope mooving the chassis on the white wheel driven by the belt from the motor. Playing one of the very long records (31’45”) showed it was played to the end and when the needle gets in the “end-spiral” (sorry I don’t have the proper word), the arm gets out of his 90° angle. I suppose this causes the lift and return of the arm to the start-position…
But wherefore is the left microswitch than? My theory: perhaps it should switch off the signal, so the lift-off noise is not audible…. because now I can hear it.
So far for the mechanics…
Concerning the sound:
I happen to have the same recording on cd and vinyl, so Iet them play parallel and switched from one to the other for comparison. The Audiolabs volume dial goes from 7 o’clock position to 5 o’clock position. I had to dial to 10 for the cd and to 12 for the record to aproximatly have the same volume. The vinyl record seems to be less dynamic and precise….somehow a bit disapointing… I noticed there is some dirt around the tube of the needle where it enters in the hole of the bigger tube (that sits in the cartridge). How to perform cleaning? Can You recommend a website where the technic of the interior of a needle system is explained? I found a lot of schemes about the magnets moving between coils, but none showed how the needletube is held in the bigger tube. I’d like to understand better how it works… I could imagine that it is held by some elastic material and that this has perhaps hardened over the years (like the belt)…
Concerning digitalisation:
The purpose is not only for the car, it also should be available on a NAS for listening at home.
So far for today
Cheers
Thanks for your feedback Sven. Good to hear that you managed to fix the microswitch after it breaking off. Good to know that this can happen too! AFAIK this end position microswitch really is used for triggering the arm lift and the successive return of the arm and the stopping of the platter rotation. That the arm lifts earlier with your sample must have something to do with another unknown problem, and it might well be the arm moving too far out of its 90 degree position. The switch is not for the mute-relay, this is switched electronically simultaneously with the arm lift on stop and delayed on start. The rope AFAIK does not have a defined start- or end position, so what is it then? Could it be a blocking of the black square plastic sliding parts that hide the cables coming from the arm? I’m sure that the issue is mechanical, and could be fixed eventually. But maybe it’s not worth the hassle if it only occurs on some records.
Depending on the recording, LP need not always sound better than CD, especially when considering forcefulness or bass-heft. The difference in level is normal unless you are using DJ cartridges. However a turntable and cartridge that have not seen any use in years need some time to come on song. When all is well, and you’re playing a well recorded album, the turntable should seduce with more fluid and free-flowing sound than typical CD while still having great dynamics and speed.
You can try gently prying with a toothpick to remove the dust. The needle system is simple and doesn’t break so easily as long as you take care not to bend the needle on either end. Indeed with MM systems the invisible part of the cantilever (the rod onto which at the far end the diamond tip is attached) is surrounded by synthetic rubber which is pushed into the surrounding tube. At the other end of the cantilever (inside the tube) is a small magnet. When inserted into the cartridge this assembly sits within 4 coils that are sensitive to the magnet’s movements. For MC cartridges this is different, but the SL7 was not meant for those and they are increasingly hard to find anyway.
If you want quality recordings then it is important to use a run-in system with a good stylus and carefully aligned arm. Check that it is at a 90 degree angle, as the electronics are old and this could have drifted. If the arm routinely jumps back to the middle position when un-cueing then you know that it is off (assuming that the rest position was aligned carefully and has not drifted). To adjust use the small torx screw at the side of the arm near where the optical sensor is. What you are adjusting is the position of the metal plate that blocks the light between emitter and sensor. Tracking force also needs to be adjusted carefully, preferably with a needle weight measure device but this requires some resourcefulness to have the platter not spinning while the arm is down (hint: I use a toothpick). If you don’t have such a device you can also adjust by ear. Know that the indicated weights are only approximate but start at the default force, I forget the value, is it 1.25 grams? Anyway, make it heavier and the bass becomes fuller while treble becomes less airy. Go too far and the sound becomes compressed. Conversely if you make the tracking force too low the sound becomes too lightweight. Somewhere inbetween is your ideal value. Between the two TT’s you have it is a matter of taste. Just try both. But remember that cartridges need to run in again after not having been used. This may take several days when playing a few hours.
I have 2 technics sl-10 turntables ,found one in a pawnshop $60 working perfectly ;2nd sl10 had to be serviced paid $275+$90=$365 in total then a bought grado black cartridge.emerson lake&palmer sounds so good on my celestion ditton 662s&442s i use in surround sound .these technic t-tables are so musical clean sounding with more open sound stage.
I have a pioneer elite vsx 92 reciever
Indeed they are nice and clean yet full sounding turntables. I think many SL1200 owners might be surprised at the quality of these underrated players.
Christiian – great articles on these linear tracking machines. I see you have dug into the inner workings of these complex tonearm assemblies and I am hoping you can help me with an issue I am having with my Technics SL-M3.
The tonearm reacts to all commands (stop, start, cue, forward, reverse searches etc.) However, the tonearm has gotten very loose and now hangs very low (i.e. tail up/nose down) while in the rest position. It hangs so low that if you attempt to play a record, the tonearm will crash into the side of the platter. If it actually makes the surface of the vinyl, it plays with terrible distortion obviously.
Again, the issue is the arm is not at the correct height or hangs too low at the rest position. The SL-M3 Service manual is not particularly useful unfortunately. I noticed in other linear tracking service manuals (SL-15 for example) the arms height is adjusted via a tonearm lift rod and there are specific instructions as to how many millimeters clearance you should adjust for. However, there is no mention in regards to an adjustment point in the SL-M3 manual.
Thanks in advance for your help.
John
Hi John, the SL7 and SL10 have an internal spring that pulls the arm to the record, and with which you also adjust the tracking force in combination with a rear-hung small counterweight. In your case it looks like there is no spring, only the weight, which is better. The lift is done with a combined electromagnet/oil-damped system and it seems that something is indeed askew in that section for your M3. This section is labelled “cueing plunger” in the manual. Just why the arm got to be so loose is a mystery, but the thing that I think you should try first is adjusting the Plunger Setscrew. As you indicate that all functions work, I assume that a manual sideways nudge still triggers arm movement as well? In other words, does the offset angle detection still work?
Additional questions: Are the bearings still intact in both dimensions? You can check this by rocking the arm back and forth (front-back) as well as rotating it around its axe, and both movements should be restricted. Perhaps it may also be worth checking the tracking force setting by means of a (digital) tracking force measuring device, not relying only on the rough scale on the player (assuming the M3 has this, as the SL7 and SL10 do).
Hope this helps as the M3 sure is a nice player!
Hi Christiaan:
Thanks for the reply and taking the time to review the service manual etc. I am going to spend some time tomorrow looking over the mechanism to see if I can spot anything awry. I too think there may be some opportunity in inspecting the set screw which the manual identifies as “tonearm set screw.”
To answer your questions: I can indeed move the arm front to back etc. while at it’s rest position. I could always move it up/down and side/side but now it is looser than ever with way too much “play.” Also – although the service manual makes no mention of it whatsoever, there is indeed a spring with a nylon screw located near the counterweight that adjusts tracking force. I keep it always at a 1.25. Thanks again for your help.
Hello, thanks so much for this great post. I’m so happy to have found it! I was replacing the cartridge on my SL-7 today and noticed that the tonearm seemed quite loose, but I don’t know if it’s supposed to be like this or not. I can push the cartridge end of the tonearm from left to right almost one centimeter, 8mm to be exact. Is there supposed to be this much side-to-side play in the SL-7 tonearm?
If the tonearm is not supposed to be this loose, what are the likely causes/fixes? Is it something I could repair myself, having no technical experience? Or would I have to search for someone in my area (if they exist) who could repair a linear tracker?
Also, if the SL-7 tonearm is not supposed to be this loose, will using the turntable with the tonearm so loose cause damage to the turntable? To the stylus? To my records? I don’t know how long the tonearm has been this way… (And I’m trying to restrain myself from using the turntable at all until I can get a better idea of whether or not something is wrong with the tonearm…)
Also, and in case it’s helpful for diagnosis: it seemed that when preparing to change the cart and I first changed the selector to 25cm and let the tonearm move there, it stopped there (and I then turned the unit off for cartridge change), but subsequently when the tonearm moved to the 25cm mark, it stopped there but then dropped. Should it drop in that situation? I also noticed that when I touched the stylus pressure adjustment screw, the entire tonearm gave easily and moved back several millimeters–is this normal?
Thank you so much for any help!
The arm on an SL7 is held up by a spring loaded metal rod with an indent into which the arm remains centered when the lift is up. On both my SL7’s the arm is neatly held in position by aforementioned rod. I can move the arm around 8mm to both sides, but not in a loose or wiggly fashion. If it really hangs loose even when the lift is up, then your spring may need adjustment or perhaps the oil damper needs work. Are you referring to angular movement or does the whole contraption move sideways linearly? The latter is not normal and may point to the string-transport needing some attention. Opening the inside of the hood is not difficult and if there’s something askew it’s usually easy to see. Some angular side play in the arm btw is necessary to allow de-centered records, and to travel to the left quickly in the lead out groove.
Great read. I have an SL-1200MK3D. After setting it up, I became interested in the SL-7/10/15 – the designs of which seemed to offset the many imperfections of pivot-tonearm turntables. My question is, how do the SL-7 and SL-10 compare sound-wise? I’ll be buying one of those models purely based on the differences in sound quality. Thank you!
The sound differences between SL7 and SL10 have been described at length in my articles so please look there for details but in short: the SL7 is more airy and nimble and the SL10 is more beefy and sonorous. Tangential tracking in principle should be better than pivot arm tracking but there are many other factors that come into play. For example you cannot mount a high end cartridge in the jacket players. A Benz ACE for example on an SL1200 will in general have better tracking of difficult or worn grooves than any P-mount cartridge in the SL7 or SL10, even better than the SAS ones indeed. Then again you might be surprised at the amount of bass and full tonality that a SL7 or SL10 is capable of, making an SL1200 sound overly clean in comparison.
Hi Christiaan, thanks very much for your rapid reply! It’s very clear and very helpful. On my SL-7, too, the tonearm is centered in the indent when the lid is up. If I stop the tonearm in the 25cm position (for cartridge changing) the arm feels quite loose and I can move the cartridge end of the arm 8mm side-to-side in an angular movement, in a motion like a metronome, or an old VU meter. Only the tonearm moves. And when I’m moving the arm side-to-side like that it comes out of the indent a little bit. Perhaps mine is as it should be, if yours, too, moves 8mm side-to-side. It’s been awhile since I changed the cartridge, and I didn’t remember the arm being so loose last time. But maybe it’s always been like this and I didn’t remember.
On your SL-7s, if you push the stylus pressure adjustment screw with a small screwdriver, do the tonearms on yours move back several millimeters?
Any idea why when I set the selector to 25cm (for cartridge changing) the arm moves to that position but then drops, and I have to immediately turn the power off? I don’t think it always did this. I think before it used to stop at 25cm, but not drop. It just started doing the stop-and-drop thing a few days ago when I was changing the cartridge.
Do you recommend any regular or occasional maintenance or servicing on these SL-7s? I want to keep this thing running forever, if possible!
Finally, have you found any specific cartridges you think sound the best on the SL-7s?
Thanks again for everything!
Sincerely,
Steven
Hi Steven, If I stop the arm at the 25cm point, leave it up (not cued), power off and open the lid then the arm is not any looser than in its start position. It does not seem loose to me. The indent in the spring still keeps it in place but you can push it past the indent left and right if you want, indeed by about 8mm, this is normal. It is also normal that the top part of arm moves forward if you press down on the adjustment screw, as the spring tension is overruled by your manual motion. It should swing back smoothly after letting go of the screw and it should only make angular movements.
Re the 25cm point: in my case setting this does not make the turntable do anything unless I also press play. Then it goes to that position and drops.
To change cartridges I always manually advance it to somewhere in the middle without letting it cue on the record, then turn off power.
While these players tend to keep on playing forever it might be good to have it checked in terms of needle pressure (VTF) and tracking error. Likely the optical sensors have gone off spec but this does not prevent it to keep working perfectly, unlike for example on a Yamaha PX2. Keep an eye on the tracking: is the arm rising straight up after playing when uncued in the middle of the record or does it always move into one direction? That might be an indication that tracking error is slightly off. Even if the reference voltages are much lower than they should be, you can still correct this with a little set screw on the side of the tone arm.
Vinylengine has the service manual so you perform some checks yourself. https://www.vinylengine.com/library/technics/sl-7.shtml
Hi Christiaan,
I have an SL-7 and would like to upgrade the captive mains and signal cables – can it be done? Is it worth doing?
Thanks, Matt
Experiments with this using other turntables suggests that this does indeed make for a difference, even the powercords, although that may have more to do with their interaction with the rest of the system than the turntable itself. In any event it depends what you want to achieve. The standard interlinks are pretty decent and don’t really need replacement but could perhaps do with new connectors. Then again you can certainly sharpen up the sound with more upscale cable, or smooth it down. Furutech and Cardas may be prime candidates. The power cable can certainly be replaced but ideally you’d have to find one that is just as thin as the current one and that will limit options to cables that will likely also sound a little thin, making it a questionanble change.
Thanks, I’ll try a new power cable first.
Hi Christiann. many thanks for your detailed and informative review. I have the Technics SL7, SL10 and SL15.. They each have slightly different mechanisms but I have been unable to measure the tracking force on any of them. You mentioned in your review thyat you had employed a toothpick to stop- the automatic lifting of the arm and allow measurement/calibration of VTF with a digital stylus gauge. However, it is not entirely clear how you did this t. Could you please give further details of how/with which turntable this approach worked? Specifically where did you insert the toothpick? Thanks.
I will post some pics at the end of the review showing how I do this.
Hi, Christiaan,
I wonder if you’ve ever examined a Linear Technics with a particular issue, a periodic low frequency noise, some sort of a “knock” sound, a “bump”. It is discreet, one only hears it on quite passages. I have the SL-10 and that happens when the arm moves a bit from outer to inner part of the record (during playback).
I’ve bought this deck used and have it since 2014. First, about 6 months ago, I thought it has appeared suddenly. But I convert albums to flacs, so I’ve checked previous conversions and the problem was there, but in 2014 it was almost imperceptible (at first only at the very end of the record side). I suppose it’s gotten worse little by little.
What would you guest as a cause for this? Old belt? Tonearm mechanism needing oil/grease/lubricants?
Would you consider too difficult for a non technician (my case) to do it alone? I have no one who would service this where I live. I have already bought the original belt (it will take a while to get it delivered).
Thanks
Dan
Hi Dan, I have not yet heard such a sound from my SL7’s or SL10’s. It will likely be something simple, but I’m not sure what. You should be able to investigate it yourself. Just make sure to obtain a new screwdriver that makes a perfect fit, to avoid damage. Although a worn belt can result in a slow-operating, or intermittently functioning arm, it should not make that bumping noise. You see, after the belt is a worm wheel meaning that the motor or its belt should not be able to directly push or pull the arm. Lubrication might be something to check. Does the arm move smoothly and with constant speed when fast forwarding in the up position manually? And does it move every 5 or so seconds during play? Or does it get stuck for a longer time, leading to the arm being off-axis?
The DL 1 cabinet top, that covers the tonearm mechanisn is actually aluminum, not plastic. I feel the SL DL1, is almost an exact copy of the SL 7, minus the quartz lock, and record clamp. I do love you article and observations, very nice article! Thank you!!
Thanks for your input Christian. I’m not referring to the lid, though, but to the upper part of the base, to which the platter is mounted. I’ve now clarified this in the article. Indeed it is said to be similar to the SL7 but soundwise I found that it sounds quite different, the DL1 sounding more like other such TT’s that use lots of plastic, such as B&O’s of that time.
Hallo Christiaan,
read your reports about SL7 and SL10. Will try your hint about the clamp some times, sounds interesting.
Since some years I use an T4P Ortofon X1-MCP high output Moving Coil on my SL7 which sounds pretty good in my opinion for the price given.
(Have no comparison to Benz´es & Co and the platform is not really comparable to your setup, but the SL7 fits in my vintage surrounding, and my wife was disturbed by the looks of the Wall mounted platform of the Project 6 that was there before – SL7 does not react to walking around on old wooden floor, pretty stable even if placed on a table, usual rack, etc.)
X1-MCP seems to be still in production according to https://www.ortofon.com/search?query=+X1-MCP , price is around 250€
The clamp removal is pretty easy and well worth the trouble, just make sure to use a new screwdriver that fits well, otherwise you may damage the screw heads. They are screwed in very tightly. Thanks for the tip re the MC Ortofon, I may give it a go one day.
Hi Christiaan,
My SL15 has recently developed the annoying habit of randomly stopping playback: sometimes halfway through playback, sometimes after 3 seconds. I don’t think it is related to the arm mechanism, as it tends to also happen when I move the arm towards the middle of the disc, keep the arm lift up for a minute and just wait… I also used the player on 12V but the problem persists.
I’ve done the forum searches: power dips, dirty contacts are all suspect, but there’s no clear answer.
Do you have any idea what might cause the issue?
Thanks.
Eric
Hi Eric, I used to have the same intermittent problem with some of my players and, like you, I just could not find what was causing it. The belts and lubrication, as well as the arm’s alignment were all good. What turned out to be the culprit is the little white switch that is depressed when the lid is closed. Due to age, corrosion and dust the switch does not always make proper contact and so the player “thinks” at some point that you have opened the lid and according to normal procedure, it uncues and moves the arm to the rest position and stops spinning the platter. The solution is to replace the switch or to simply flick it in and out repeatedly by hand, making sure to press it a little deeper than normal. For me, this did the trick. The best part: if you are not replacing it you do not have to open the player as the switch is accessible from the top.
That is a great answer! I never would have come up with that one myself.
I have tried it and so far so good, no more interruptions.
Thank you!
Glad to hear that it worked. To be honest, I could not figure it out either until a repairs person told me this when I bought another turntable from him and I mentioned it in passing when I spotted a couple of SL10’s on his shelves.
Well you’ve been very helpful, no matter where you got your information from!
Might you also have the answer to an issue with the muting relay only working on one channel? I guess it is stuck because the arm drops quite audibly on the record, but only on the left channel…
The single channel muting will likely indeed be caused by the mechanical muting relay being dirty or worn. Some of my players occasionally also have this but it seems to only happen when they have not been used in a long time. You could replace the relay or just not worry about it as it is not vital for operation and for convenience only. All the relay does (I assume) is to short the cartridge output to ground during arm lift.
Do you know where the mechanical muting relay is located inside the SL-15?
I’d like to take another look at it, if only I knew where to look 🙂
Hi Eric, I’ve not yet looked for it myself but as I understand it reading topics about this, the mute relay is a RL-601 STDP Reed relay. Note that this is a sealed glass unit that on the outside may look like an ordinary black IC, IE not like a traditional plastic relay. Even if you located it, there would be nothing you could do to service it unless you intend to replace it. The relay is apparently on the main board under the platter. Also note that it only shorts the signals to ground, they do not normally pass through it.
Hi Christian,
Do you have any useful tips to replace the damping fluid in the SL15 arm? The arm on my 15 just drops on the record. I’ve looked at the service manual and exploded view but it hasn’t gotten me any further yet…
Hi Eric, I’ve yet to encounter this issue myself on any of my players and assuming that the mechanism is not broken, what might have happened is that the dampening mechanism of the cueing system was inadvertently lubricated while greasing something else inside. In that case the damping mechanism has to be cleaned and a fresh amount of silicone fluid has to be applied to the plunger. There is no reservoir, the fluid is applied to the middle part of the plunger and the system relies on the fluid being of high enough viscosity to drop the arm slowly. A quick online search leads me to the mention of very thick, paste-like, 300.000 to 500.000 cst silicon oil which should work well with all Technics turntables.
Hi Christiaan, thanks for the quick reply! My issue, however, is where to clean and reapply the oil. In other words, where is that middle part of the plunger?
Hi Eric, I have sent you two images on which you can see the metal plunger and its rotational mechanism. I have not taken the arm apart any further than you can see in these images but you just need to investigate where the rotating part has potential for friction/viscous damping with its surroundings and that’s where you need to apply the damping fluid. As I mentioned, there is no reservoir as you may expect.
Christiaan, what a great article, enjoyed reading it.
I’ve got a 70’s Rega Planar 3 with a broken R200 arm. I fell in love with the SL-7 when I came across one at an airbnb stay in Stuttgart last year.
I guess my question is: Repair the R200 or go SL-7? I don’t really want to make it any more complicated than that. I’m mainly listening to soundtracks in a less than ideal room, 70’s Celestions and a 90’s reference amp from Teac (500i). I’ve never heard the Rega as it was given to me by a friend in the current condition.
This is a personal matter. Some people seem to really like the Rega sound but I personally don’t and think the SL7 sounds much more refined, as long as a good needle is used, preferably Jico SAS or similar. Even a standard Jico is better than most no-name replacements. Do note that the Technics is getting really old and that at some point a repair might be required. That said, I have had several SL7’s and SL10’s and they proved to be extremely reliable.
Thanks Christiaan – will take look at those styli.
Hi Christaan,
I now have an SL10 and SL15 with intermittent cuts due to the lid microswitch issue. Would it be a good idea to not replace the switch but bypass the switch by connecting the contacts on the board directly?
Kind regards
Eric
Hi Eric, that’s actually a good idea! The only feature that I imagine you would then miss out on is the automatic parking of the arm when opening the lid, otherwise, it should work. For me, just deeply depressing and releasing the switch 20 or so times with a pointy item always did the trick. You may also consider cleaning the switch with contact spray or taking it apart and actually cleaning it.
What I did as an intermediate solution is take a piece of tape and put it on the inside of the cover before screwing the inside cover back to the lid. That way, no soldering or bridging of contacts is necessary… and it’s doing the trick so far. The switch is permanently pressed as it is when the lid is closed… fingers crossed!
haha, that sounds like a great solution, too:-)
Hi Christiaan,
I enjoyed both parts of your article, which I’d only just discovered, though they were apparently written nearly six years ago. I have an SL-DL1 myself – well two actually, on different hi-fi systems, and an SL-L1 as back-up. Both of my DL1’s have had an issue with the microswitch mentioned in the comments above, where they just ceased to play at all, and I have had both switches hardwired, by a hi-fi engineer I use for repairs & servicing, so the turntable thinks the lid is closed, even when it isn’t, and so plays. It’s a pointless switch in my view anyway, as I wouldn’t ever be opening the lid while it’s playing. I’ve also had both of them professionally serviced by the same engineer, with new belts on the tracking system, etcetera.
I was interested to note your criticism of the plastic part of the DL1 body making it sound less luxurious, because I’ve never found that. In fact I didn’t even think it was plastic, as the body feels cold to the touch, like metal, apart from the see-through part of the lid, but I’m sure you’re right. Hence, I’m wondering if my belief that mine sounds so good, might be because of the cartridge & stylus I have?
I’ve always thought that the cartridge is the single most important part of the turntable, in terms of sound quality, closely followed by the tracking mechanism. For the rest of it, the key points to me, are no appreciable rumble or wow & flutter. That’s oversimplifying it of course, but I love the DL1 because it tracks brilliantly, has no rumble and no appreciable wow & flutter.
Anyway, I managed to break the stylus cantilever on the DL1 on my main hi-fi, and I didn’t know if I could get a replacement stylus at the time, so I decided to have a complete cartridge upgrade instead – literally. I sent the whole cartridge off to Van Den Hul, had them gut it – coils, magnets, cantilever and stylus, everything – and refit the shell entirely, with all their own parts.
What came back to me was the best moving-magnet cartridge I’d ever heard, and it still is. Honestly, that luxury you were commenting about was suddenly all there, with much greater depth & detail then I’d ever heard before. Then, when I relatively recently upgraded the amplifier, from a Yamaha A595a to a Denon AVR-3083, the Denon showed even more of what this cartridge is producing. It’s as if the amp was then the limiting factor – not the cartridge or the turntable or the speakers – and the Denon seems to do everything justice, like the rest of the system always deserved.
I know that VDH have done the same custom cartridge upgrade for some other DL1 owners too, but they’re very rare – partly because it’s a very fiddly job, cramming their stuff into the existing shells! I was asked never to break it – please! ?
I’ve always regarded the Revox B291 to be the king of linear tracking turntables, though I was never able to afford one, but with that custom VDH cartridge, I actually think the DL1 might be near enough! All of which now leaves me wondering what on earth it would sound like on an SL7! ?
Kind regards,
Marcus.
Hi Marcus, the SL-DL1 has a metal top but a plastic chassis. You’re right – the cartridge will make all the difference. But even then, there are differences in timbre among these Technicses. Then again, this is something that I tend to pay special attention to. It’s quite amazing that all the little Technicses that I owned and used all still play perfectly after all this time. That’s really great engineering! Interesting to hear that you did a vDH retip on this player and good to read that it works so well. Haha, yes, Aalt-Jouk is a nice guy with a great sense of humor. Indeed, I think very few people will have gone to such length, most not having gone beyond the basic replacement styluses and thus have never heard what these machines are really capable of. They probably just look too cute for the mainstream to take them as seriously as they deserve. For me, the SL7 and the SL10 sound more solid and “mature” than the DL1. I’ve also been eyeballing the Revox but always felt that it would be too fiddly with its ultra-short arm. I read somewhere that it sounds inline with the other turntables of its sort but don’t know how much trust I should place in that comment. Alas, I have never heard one in person.
Hello! I have just got me a SL-15. I wonder if you have had any problems with the clamp when you play the record with the lid closed completely down? I hear squeaking noises from the clamp rotating and the music is out of pitch. When I open the lid a little bit, so it is not completely closed, I do not hear any noises and the pitch is correct and fine. May it have something to do with the thickness on certain records or is the clamp misadjusted? ALSO; if I play with the lid a little open as I do, will the tracking and needle pressure still be correct? Hope to hear from you! All the best!
Fixing the problem you describe will involve adjusting the height of the clamp container or an element within it. Maybe the ball bearing has come loose? Or the screws have come partially loose? When opening the lid, even if slightly, you change the arm’s VTA and, thus, the tracking. Depending on the complexity of your cartridge’s needle shape, that can lead to audible results. The easiest thing to do is to remove the clamp altogether. You can remove it by removing the black inner part of the top cover. Take care to unscrew all the screws, there are many! The bonus for fixing your issue is that this will sound better!
Hello Christiaan, did you ever evaluate the Technics SL10 with the original MC310 cartridge? If so I am curious to your findings.
Hi Bert, I did, but I think the sample was too old to really represent how it once sounded. In short, it sounded a little warm and muffled and lacking vitality. Also, I strongly feel that today’s Jico SAS stylii are simply superior. Ultimately, a stylus’ shape is more important than the relative advantage of using a moving coil instead of a moving magnet.
Thanks Christiaan, it helps me to decide to go for a vintage MC310 sample or not right now.
No probs, Bert. I’m sure the cart was great in its day and when new, but the reality is that the suspension alters its properties over time and if you ask me this cart really is a little too old. Asides from the fact that it is near-impossible to find one with a stylus that, after all these decades, truly is still in great shape.
I have a source that has 6-7 of these carts on offer claimed to be in very good and original shape. He shows pics with coils measured excellently. He claims they sound great as well. Still the quality of suspension is still questionable after 45 years as you rightly noted.
Age aside, it’s also a case of preferences. The 301 sounded warm and sweet to me whereas a Jico will sound clean and articulate.
Hello,
I recently get one sl-dl1, but the cord moving the stylus is broken.
So, I bought some fishing rope, but, I don’t have any idea of the size of the rope. Does anyone have any idea?
I tried with my feeling, but the stylus keeps scratches, and is making a crack while playing.
Thanks a lot for your advice
Regards
I would suggest sourcing another DL1, even if it is broken in another way, as an example. Or alternatively get any cheap Technics linear tracker on the side as a guide. Otherwise, you may be in for A LOT of trial and error.
Hi Christiaan
Good morning ! First sorry for my english (I’m french) I have a technics SL 15. I try to repair it after years of storage . I have replaced the belt by a new one cleaned and oiled the rails then starting a LP the plate start to turn but the arm does not move foreward I also also tried to select a band using the switch on the top cover then the light turns red the arm move foreward up to the end then return then light turn off then pushing the start button nothing happen. I suspect the optical sensor .How to check if it works ? Any advice Please Can you help please ? Have a nice day A TRUCHI atruchi@gmail.com
The photo sensor only comes into play once the arm is queued and playing. If the arm motor does not move even from its resting position then there must be an electrical fault elsewhere. Alas, I would not know where.
Hello I am looking on how to repair my SL-L24 turntable but it seems to be an unknown model could use a manual for a start
Any help would be greatly appreciated
Alas, I have never seen the SL-L24 nor do I have a manual for it.
Hi Thanks for your response . I used your l20 post as a guide as it seemed very much the same and managed to get it to work again.
I bought it new way back when and it has been in use ever since.
So can’t complain. Would buy a new one if they still made them
Regards
Peter
Thanks for the write up. Stumbled across as I was researching a Technics SL-J92 which has a similar mechanism. Have a SL-5 waiting in the wings and just cleaned up/adjusted a Realistic linear tracking turntable. Was interesting to watch the voltage feedback as the stylus lateral displacement (pressure, whatever) increased until the motor adjusted the arm position.
Too many old turntables to bring back to life – excited about my Columbia 360 (US version of Pye 1005). Highest “cool” factor of anything I have but horrible electronics (they used to rectify AC with what! – Selenium?)
I am the proud owner of a Technics SL-L20 linear tracking belt drive turntable and an Audio Technica AT-LP120 Direct Drive USB Turntable. I tend to surf the bottom of the line. However, as well as I have the LP120 tone arm and cartridge set, the outer, and especially the inner tracks of LPs sound better, cleaner, with deeper bass and crisper transients on the L20. While I haven’t tried either with moving coil cartridges, the M100 sure on the L20 is a step down from the VM95EN to wh9ich I upgraded on the LP120.
I looking at a B&O 5005 turn table, also belt drive, that needs a new cartridge. I can pick up the turntable for about $50 – it’s in perfect working condition with a new belt – but I can’t find a cartridge for less than n$250. So, I’ll be locking for a while.
I have a Telarc recording of the 1812 Overture. I have never found a turntable that is capable of tracking the inner grooves without distortion. That’s where the canon fire and carillon bells are played. The L20 does it better. I can’t speak to perfect (using the CD as a reference is folly because the transcription was flawed for those pieces and Telarc never brought out the recording in SACD).
Thanks for the article. I too started with a J3 and just fixed an sl10.
Christian,
Your article is great. Thanks for the information. Between the comments section, especially your answers, and the information in the article, you’ve created what could be considered a USER’S GUIDE and a BASIC MAINTENANCE MANUAL, both of which are critical for owners of vintage gear.