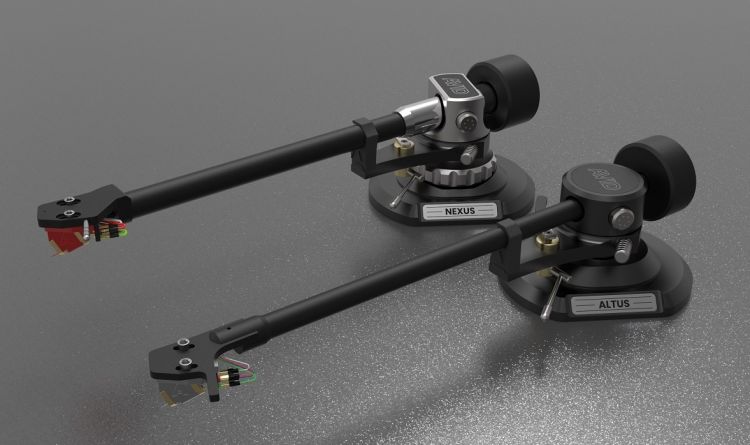
Technical Aspects
The headshell wire clamps of both tonearms fit intentionally very snugly onto the BORON’s pins, obviously making for good connections but requiring extra care when pushing them onto the cartridge. To facilitate easier initial fitting and opening of the clamps, AVIDHIFI cartridge pins are pointed at the ends.
If desired, the user can use an Allen key to slightly open up the pins at their entry point but my instinct would be to leave them nice and tight. As AVIDHIFI’s Stuart confirmed, one need not worry about damaging the arm’s bearings when holding it in place while pushing the clamps in place. But of course, always do this with the protective cartridge cover in place.
A purpose-designed low-capacitance external phono cable reassuringly anchors into place using a right-angled DIN connector and high-quality gold-plated RCA plugs. For purists wishing to embrace the naturally balanced output of a phono cartridge, the cable is also available fully balanced with XLR connectors.
Both arm boards have a 3-point connection for ideal rigidity under all circumstances. To this end, the hole in the arm board has an internal egg-like side. You can’t tell from the photo but the inside of the hole is vertically machined such that the sole point of contact with the arm shaft, after fixing the side screw, is in the vertical middle.
One might not notice it upon casual inspection but the lift system itself is 100% proprietary, right down to the tiniest components. Whereas 99% of the other companies use OEM parts made by one or two big manufacturers, AVIDHIFI chose to fabricate their own bespoke lift system. Rather than relying on the resistance of oil, which can vary according to ambient temperature, making the lift go slower or faster depending on the room temperature, AVIDHIFI opted for a spring-loaded system. Unlike traditional systems, the spring-loaded lift will always move at the same speed, regardless of room temperature. An additional feature of this system is that the lift moves slower for the last portion of its travel, providing a particularly soft landing for the cartridge.
The arm lift platform has an unusually compliant foam layer on top. Usually, this pad is made of harder rubber but with the AVIDHIFI tonearms, the rubber is so soft as to cave in quite deeply when the arm is resting on top. As it was my first time encountering this, I asked Stuart about it. As it turns out, the thought behind it was ergonomics, chosen for the extra resistance and confidence, for a nice feel while cueing (and to prevent large sides). While I agree that the headshell will indeed absolutely never slip inadvertently, I also feel that the compliant foam makes tiny cueing corrections harder than normal.
When mounted with the VTA such that the arm is level with the LP surface, and with the arm lift in its uppermost position, the arm only goes just about high enough to clear the stylus from the digital scale’s weighing platform. Since the arm lift uses unusually compliant foam, it’s worth being extra careful when traversing such objects on the platter’s surface.
There is no dimple in the horizontal center of the gimbal housing which makes adjustment via a one-position protractor such as the Acoustical Systems SMARTractor that I like to use less convenient. I wondered, was this omitted on purpose? Stuart responded that the supplied two-point protractor can be used which requires no location in relation to the arm pivot point and that this protractor is well-tested and considered ideal.
Neither arm offers an Azimuth adjustment facility. As I found in practice, styluses need not always be mounted 100% straight in the cantilever so I feel it is good to have a facility to correct for this. Upon inquiring as to why this was omitted, Stuart Robertson of AVIDHIFI responded that the tolerances in the AVIDHIFI cartridges and arms are very tight, essentially assuring proper Azimuth from the factory. Upon insisting, he added that the company feels that a relatively small number of people have the required tools or skill to properly adjust the Azimuth and it’s more likely to result in an ill-adjusted cartridge than it ending up just right. While I agree that he makes a fair case and most users would probably indeed not want to fiddle with this, I would still expect a tonearm in this price range to offer the facility for those who wish to adjust it.
When handling the tonearms manually, I noticed that they are more restricted in their vertical movement than normal, due to how the bearing housing is constructed. Naturally, the arm has ample freedom for cueing and tracking the record. I asked Stuart if this restriction is intentional. Of course, I needn’t have asked, indeed, it was intentional and done because the less bearing movement, the more rigid the arm is. The reduced freedom provides a smaller window of potential play.
Both tonearms are supplied with perfectly-fitting arm boards which are screwed in place from underneath the chassis extension. The geometry is made for a pivot-to-spindle distance of 216mm rather than the commonly used 222mm.
Stuart Robertson of AVIDHIFI explains tonearm geometry
“There is not really a norm when it comes to geometry. While many manufacturers adopt a geometry model to match that of others to help facilitate easy drop-in replacements and help economize on design time and cost, our expertise, and on-tap precision manufacturing plant, have allowed us to not just settle for what those before us have done, but instead, (as we do with everything we design), start with a blank sheet of paper and design a product that is the absolute best possible without limitation or constraint.
The 216mm distance was selected as an integral part of an overall geometry that allows keeping the arm shorter for increased rigidity, while also allowing a lower moving mass. This lower moving mass reduces the inertia of the tonearm, resulting in an ideal balance between rigidity and tracking performance, ultimately leading to lower tracking distortion. This “shorter” length is crucial to keeping unwanted resonances in the arm to negligible values.
The Pivot to Spindle (Mounting Distance), Tracking Angle (Offset Angle), and Overhang, together with some other elements make up the overall geometry. It’s the overall geometry that makes the difference, and that’s where the magic happens!”
Side By Side Comparisons
Here are the two counterweights shown side by side. On the left is the ALTUS and on the right is the NEXUS. Note that the NEXUS weight has the same outer diameter but has a wider diameter hole to fit the thicker arm. To compensate for this, it is wider/thicker in shape.
System Context
The tonearms will be reviewed in combination with an AVIDHIFI BORON cartridge and an AVIDHIFI Sequel SP turntable in the Main System. The rest of the analog chain consists of a CH Precision P1 phono preamp, L1 preamp, A1.5 power amp, and Magico S1 MkII speakers.
Tonearm and Cartridge Setup
The tonearms are easy to mount thanks to their perfectly-fitting arm boards which are screwed in place from underneath the chassis extension. For cartridge setup, I used the Acoustical Systems SMARTractor protractor with its Loefgren B DIN setting. The VTA (Vertical Tracking Angle, or effectively the tonearm height) was adjusted such that the cartridge’s body and the tonearm tube were visually parallel to the record. Then, the cartridge’s overhang and zenith (horizontal rotation in the headshell) were set using the SMARTtactor, followed by the VTF (Vertical Tracking Force) to my earlier established ideal of 2.27 grams.
Next: Listening and Conclusion